「Palit」のグラフィックカードはこうして作られる Palit 30周年記念 工場見学レポート
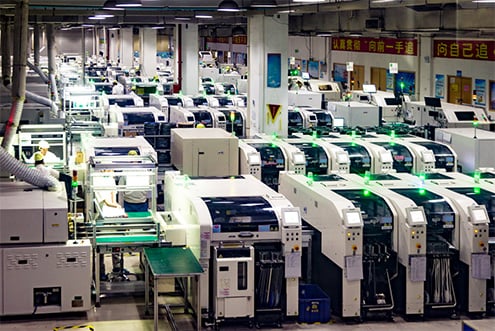
「Palit」のグラフィックカードは
こうして作られる
Palit 30周年記念
工場見学レポート
「Palit」はドスパラが直販しているグラフィックカード製品を開発しているメーカーです。ドスパラは2007年からPalitと代理店契約を結んで以来、日本で唯一Palit製品を販売する窓口となっています。
Palit製品の魅力とは?
Palit製品は一般向けのリーズナブルな製品からゲーミングシーンに特化したハイエンドモデル「GameRock」シリーズまで幅広いラインナップを揃えています。これらの製品はPalit独自の技術で設計され、常に最新の技術を導入し続けている工場で製造しています。
Palit製品の強みを抜粋すると下記の通りです。
・特許取得済みの独自冷却技術「TurboJET4」
・手軽にオーバークロックができるソフトウェア「Thunder Master」
・オーバークロックに失敗しても安心な「デュアルBIOS」
・サーバーマシンなどにも採用されている省電力技術「DrMOS」
具体的にそれぞれの内容を見ていきましょう。
現代のグラフィックカードを支える技術として冷却性能技術は欠かせません。いかに製品を効率よく冷却し、かつ静粛性を確保するかが優れた製品を開発する鍵となっています。
Palit製品もこの点、抜かりはありません。たとえばPalit製品のフラグシップモデルに採用されている独自冷却技術「TurboJET4」はその技術の粋を集めた冷却機構で特許も取得しています。
グラフィックカードは冷却性能が高ければ高いほど優れたパフォーマンスを発揮します。これはグラフィックカードのコアとなる「GPU」(Graphics Processing Unit)が自身の発熱量に応じて動作クロックを調整しているからです。つまり冷えれば冷えるほどGPUは高いクロック数で動作し、パフォーマンスも高くなります。
「TurboJET4」の特徴はなんと言ってもアンチボルテックス効果を導入したデュアルダブルファンです。TurboJET4を搭載したグラフィックカードは外見上2つのファンを搭載しているように見えますが、実はそれぞれのファンは2重になっており合計4つのファンを搭載しています。
さらに、二つに重なったファンはそれぞれ逆方向に回転します。実はファンの形状も外側と内側で異なっており、これによって空気の流れを集中して冷却効果を高めつつ、風切りノイズを打ち消しあって静音性も確保するという画期的な仕組みになっています。Palitではこの効果を「アンチボルテックス」と呼んでいます。
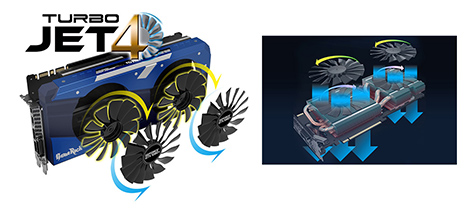
オーバークロックも安全に試せる
高い冷却効果を得られるなら、オーバークロックも試したくなるものですが、Palit製品には手軽にオーバークロック設定を楽しめるソフトウェア「Thunder Master」も付属します。
「Thunder Master」では簡単な操作でGPUやメモリの動作クロック、動作電圧を調整できるほか、あらかじめ「OCモード」「ゲーミングモード」「サイレントモード」という3種類の動作モードも備えており、用途に合わせてワンクリックでモードを切り替えることもできます。
しかし、オーバークロックにはリスクもつきものです。オーバークロック設定に失敗してグラフィックカードが起動しなくなる、という可能性もゼロではありません。
そんな場合に備えてPalit製品の多くには「デュアルBIOS」機能も搭載しています。この機能を搭載するモデルはあらかじめ二つのBIOSを持っていて、通常は片方のみを使って動作しています。
そのため、設定に失敗してグラフィックカードが起動しなかった場合にも、本体裏にあるスイッチを切り替えることで通常のBIOS設定に戻すことができ、その状態で起動すれば設定に失敗した側のBIOS設定を修正して通常通り使用できるようになります。「デュアルBIOS」は万が一に備えるための保険になる機能です。
このほか、サーバーシステムなどにも使用される省電力機能「DrMOS」に対応したチップを搭載するなど電源周りの設計もこだわり、安定した動作を実現しています。
これら以外にもさまざまな技術が使われていますが、こうした技術の積み重ねにより、Palitのグラフィックスカードは常に最高の性能を引き出せるように設計されているのです。
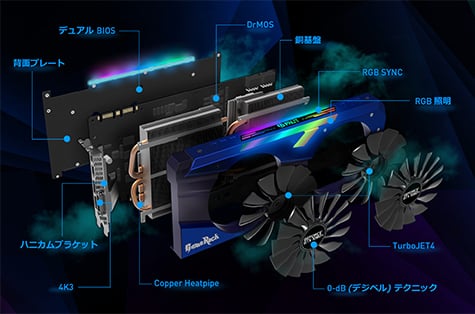
高いコストパフォーマンスの秘密
Palit製品の魅力はハードウェアの性能だけではありません。その高いコストパフォーマンスにも魅力があります。
グラフィックカードは海外から輸入されることが多く、一般的には輸入代理店が間に入ることで日本全国に流通します。そのため販売価格には輸入代理店の中間マージンが入るため割高にならざるをえません。
Palit製品は輸入代理店を経由せずドスパラが直販しているため、中間マージンがありません。そのため他社と同等の価格の製品でもより高性能なものを提供できることが特徴です。
極端に安価な製品は、安いパーツを使うなど必ずどこかでコストダウンをするものですが、Palitの製品は製品自体のコストを下げることなく高品質の製品を販売できる、ということになります。
「Palit」は今年で30周年
実はPalitの歴史は意外と古く、1988年に台湾で設立されました。今年でちょうど30周年を迎えます。古くからグラフィックカードを中心とした製品を製造していますが、その名前があまり知られてこなかったのはOEMメーカーとして世界の有名PCメーカーに製品を供給していたためです。
Palitは契約上、取引のあったPCメーカーを明らかにしない事が多いですが、多くのPCメーカーやサプライヤーに製品を供給していました。
そのため、「実はPalit製のパーツが組み込まれていたパソコンを使っていた」という人は少なくないかもしれません。
今回はPalit創立30周年記念ということでPalit製品を生産する工場を見学する機会が得られました。Palitの工場が外部に公開されるのは創業以来初めてのことです。Palit製品がどんな工程を経て作られているのかを見ていきましょう。
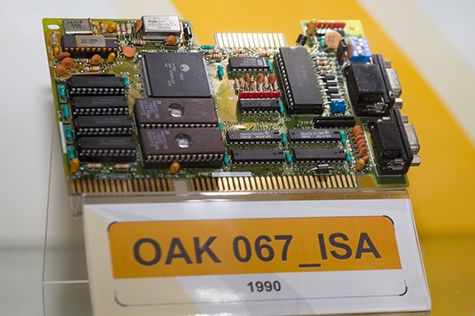
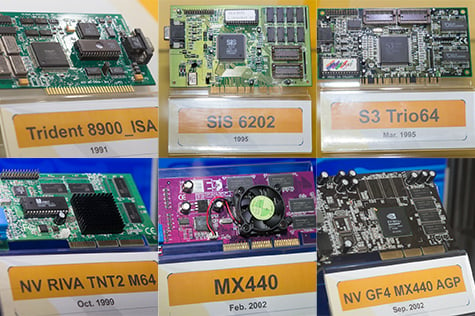
最新の生産設備を備えたグラフィックカード工場
Palitの本社は台湾にありますが、工場は「中国のシリコンバレー」とも呼ばれる中国の「深圳(シンセン)市」にあります。「Pilot Electronics」と「Tai-Hui Electronics」の2つがそれで、いずれもシンセンの中心街から高速道路で40分ほど北上したところにあります。Palitはこのほかにも複数の外部委託業者と契約をしていますが主力となるのはこの2つの工場です。
Pilot ElectronicsはグラフィックカードのみでなくOEM向けのマザーボードやスマートフォン向け製品の製造なども行っている工場です。グラフィックカードは年間100万枚、マザーボードは年間400万枚の生産力を持ちます。
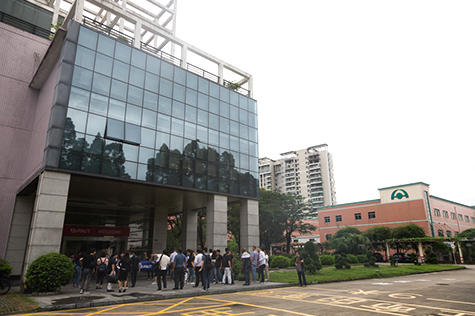
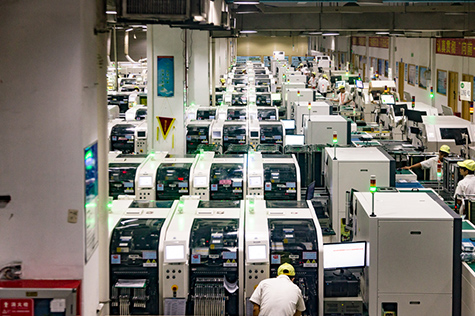
一方のTai-Hui Electronicsはグラフィックカードを主力とする工場で年間300万枚の生産数を誇ります。今回主に見学したのはこちらの工場です。
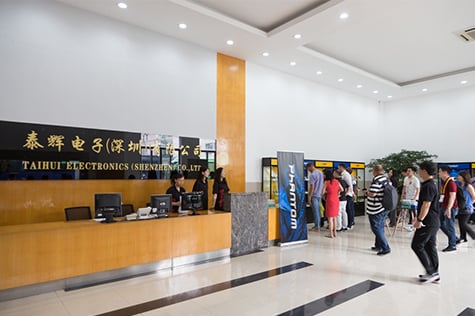
製品製造の要となる「SMDライン」
グラフィックカードの製造工程で最も重要なのが「SMD」の工程です。
SMDとはSurface Mount Device(表面実装部品)の略で、基板に穴を開けることなく基板表面に電子部品を実装する「表面実装技術」で使われる部品のことです。
この技術ができる前は基板に部品を取り付けるためには、基板に穴を開けて部品から生えているピンを差し込み、ハンダ付けをしていました。
しかし、穴を空けるとそのぶん基板の強度が弱くなってしまいます。また、部品自体も大きく一定の間隔を開けて部品を実装する必要があるため、部品の実装密度には限界がありました。
表面実装技術では基板に穴を空けることなく直接基板上に部品を取り付けられるので、より多くの部品を高密度に実装することが可能になりました。現在ではグラフィックカードに限らず高密度に部品を実装する必要がある最新のデジタル機器では一般的な手法です。
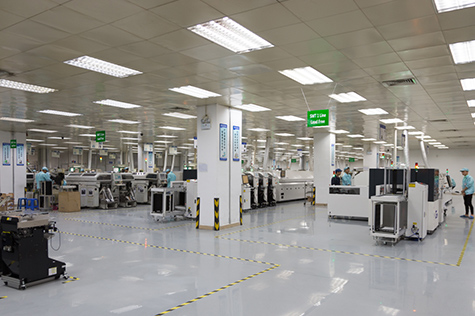
一般的なSMDラインは主にはんだ印刷機、部品実装機、リフロー炉という3つの機械で構成されています。PalitのSMDラインでは、印刷機および実装機にパナソニックの表面実装機「NPM-D3」を使って部品を自動的に実装しています。
NPM-D3は2018年に導入されたばかりの機材で、Palitでは常に最新の機材を使用して製品の製造を行っているそうです。
SMDライン工程ではまず基板上の部品実装箇所に「クリームはんだ」が印刷されるところから始まります。この工程はまさに「紙にインクを印刷する」工程に似ていて、インクの代わりにクリームはんだを印刷(塗布)するイメージです。非常に小さな部品にも対応するため微細な技術できめ細かくクリームはんだが塗布されていきます。
次に印刷された「クリームはんだ」の上に部品を配置していきます。SMD工程で扱う部品は非常に小さいためテープ状に並べて取り付け、それをリールに巻き取った状態のものを使います。表面実装機はテープに取り付けられた部品をノズルで吸い上げて基板に載せる、という作業を自動的に行います。
表面実装機には2種類あり、GPUやメモリなどの大型部品を実装するものと、それ以外の小型の部品を実装するものがあります。大型部品を取り付ける実装機は毎分600個、小型部品を取り付ける実装機は毎分1400個もの部品を実装する能力があります。
ちなみに、はんだの印刷工程で使われる「クリームはんだ」は、はんだとフラックス(ヤニ)を混ぜたもので柔らかく、粘着性があるため、その上に部品をのせると一時的に部品がクリームはんだ上にくっつきます。クリームはんだは加熱すると熱によってフラックスが気化し、溶けたはんだのみが残るため、そまま冷えればはんだが固体化するので、部品を基板に固定できる、という仕組みです。
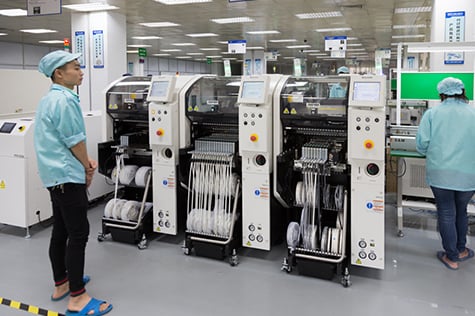
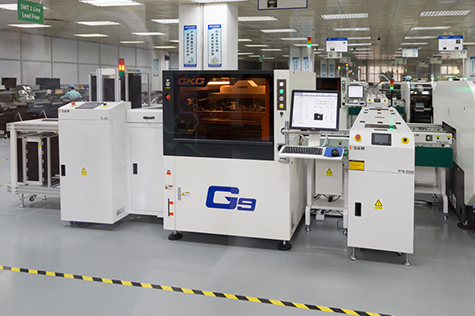
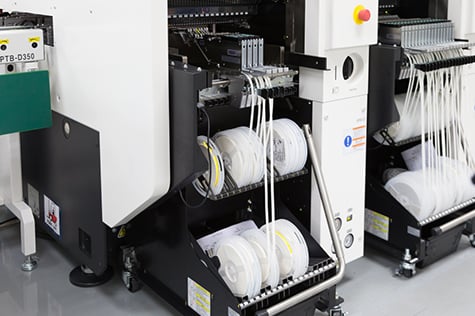
基板に印刷されたクリームはんだを熱で融解して固定させるための機材が「リフロー炉」です。リフロー炉の機能は簡単に言うとオーブンのようなものですが、不用意に加熱しすぎると基板や部品を傷めてしまします。そのため加熱する材質に合わせて細やかな温度管理が可能になっているのが特徴です。
リフロー工程が終わると「AOI」と呼ばれる機械の出番となります。AOIは「Automated Optical Inspection(自動光学検査装置)」の略でCCDカメラなどを使った画像認識によって自動的に部品の実装ミスを検出できる機械です。非常に精密な誤差まで検出できるため人間の目では検査しきれない細かいズレも見逃しません。これにより製品の歩留まりを改善しています。
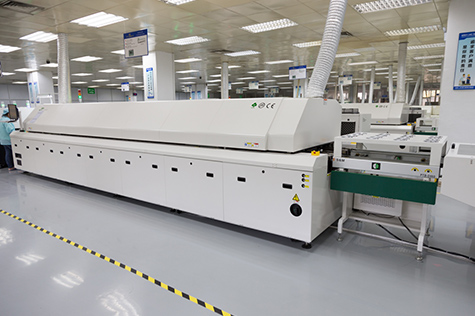
DIP工程と冷却ファンなどの取り付け
精密部品の取り付けが終わると、次は「DIP工程」へと進みます。
DIP工程ではSMD工程で実装をする必要がない部品の取り付け作業を行っています。DIPとはDual in-line Packageの略で、四角い半導体部品の両サイドから多数のピンが生えている部品を指す用語です。
DIPで実装する部品は比較的大きめの部品が多く、人間が手作業で基板の穴に部品を差し込んでいきます。その後「ウェーブソルダリングマシン」によって自動的に半田付けされていきます。ウェーブソルダリングマシンは基板の裏側に飛び出した部品のピンに極小のノズルを使って半田付けを行う機械です。
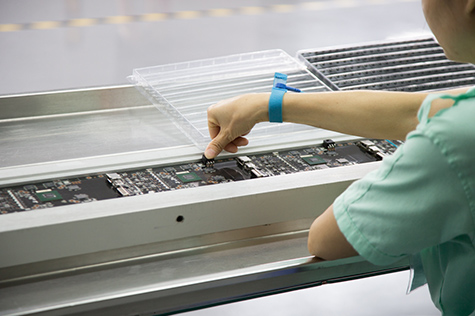
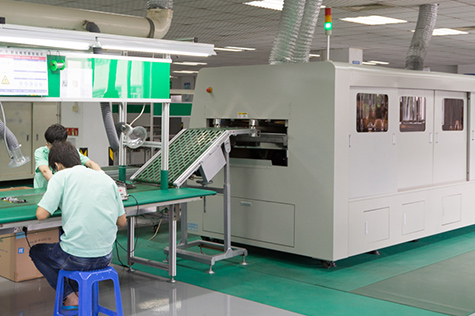
DIP工程が終わると冷却ファンやブラケットなどを熟練工が手作業で丁寧に取り付けて行き、いよいよグラフィックカードが完成します。しかし、ここで終わりではありません。
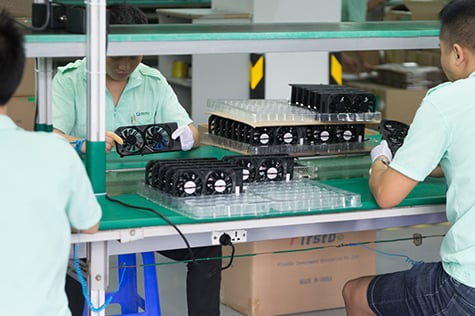
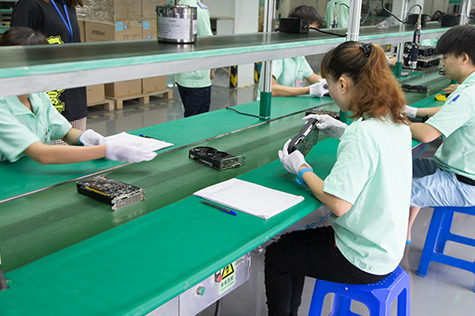
確実な動作検証と過酷なテスト
グラフィックカードが完成するとすぐに検査工程が待っています。全ての出荷製品に対して「3DMark」など、お馴染みのベンチマークソフトを使った動作確認や出力ポートの動作検証を行います。
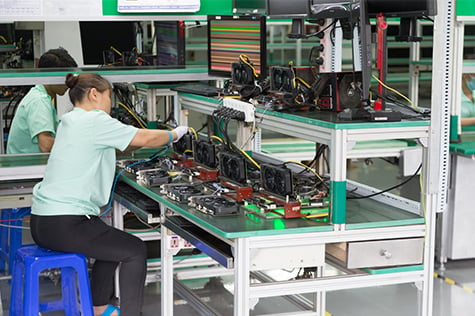
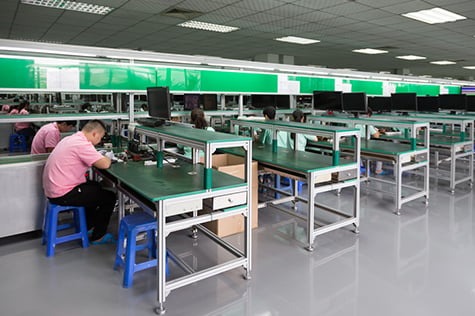
通常環境での動作に問題が無いことを確認すると、次に過酷な環境下での動作を確認するため「バーニングテスト」が行われます。
バーニングテストは新製品の場合は発売後3~4ヶ月間は全ての出荷製品をテストし、その後は抜き打ちでのテストが実施されます。
テストは室温45度Cを維持する恒温槽内に製品を搭載したパソコンを設置して行います。テスト中は3DMarkを動作させ、最大4時間の負荷テストを行うことで想定内の負荷であれば製品が問題なく動作することを確認します。
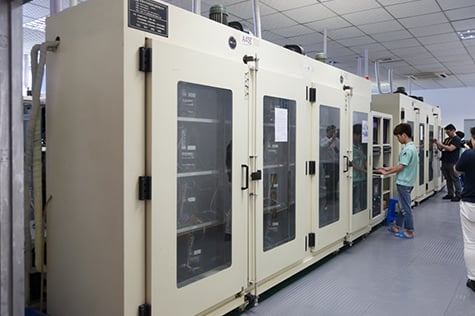
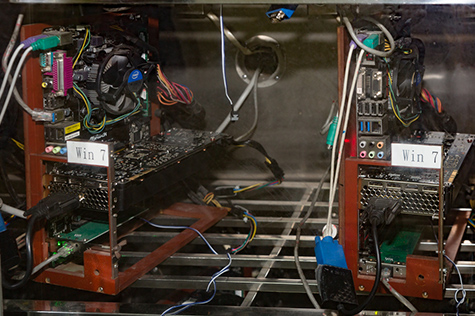
こうしてテストを通過した製品は最後にパッケージングの工程に流れ、人の手によって丁寧に包装されて出荷されて行きます。
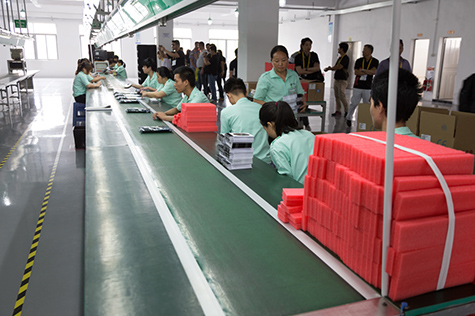
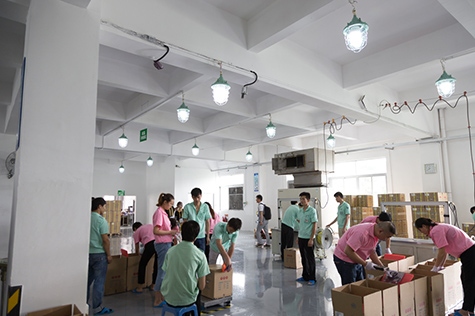
相反する要素を追求して良い製品を
以上がPalit製グラフィックカードができるまでの流れです。Palitのグラフィックカードは最新技術を使った設備と機械による自動化と、人間による入念なチェックをクリアした上で出荷されていることがわかると思います。
工場見学を終え、Palitにあらためて同社製品のこだわりについて聞いてみました。Palitでは「グラフィックカードは『より速く』『より冷却性に優れ』『より静かに』をコンセプトに製品開発をしている」といいます。
しかしこれらはそれぞれ相反する要素でもあります。より速くだけを追求すればGPUの発熱は増大し強力な冷却性能が必要で騒音はうるさくなります。冷却性だけを追求するなら性能を低く抑えて発熱を低くすれば実現できます。しかしこれでは意味がありません。
こうした「相反する要素」を独自の冷却機構やオーバークロック技術を組み合わせ、限界まで詰めていきながら消費者が手頃な価格で購入できる製品を開発することがPalitの使命であると考えているそうです。
ドスパラが日本でPalit製品の直販を初めてから11年が立ちました。ドスパラはこれからもPalitのパートナーとして高性能な製品をより安価に提供していきます。